For centuries, man has recognized the need for windows. Whether they were a simple opening used to promote ventilation, a roughly covered area to get the jump on unwanted company, or a glazed pane used to enhance the aesthetics of the building, windows have been a useful component to the home.
As we’ve seen throughout history, innovations in technology have helped update and enhance every aspect of the window. Today’s products address problems related to functionality, appearance, cost effectiveness and efficiency. In addition, new and improved materials, manufacturing methods, and installation techniques have contributed to making current window offerings the best ever.
To better understand why replacement windows are designed the way they are today, we must first see how they’ve evolved:
Early Beginnings
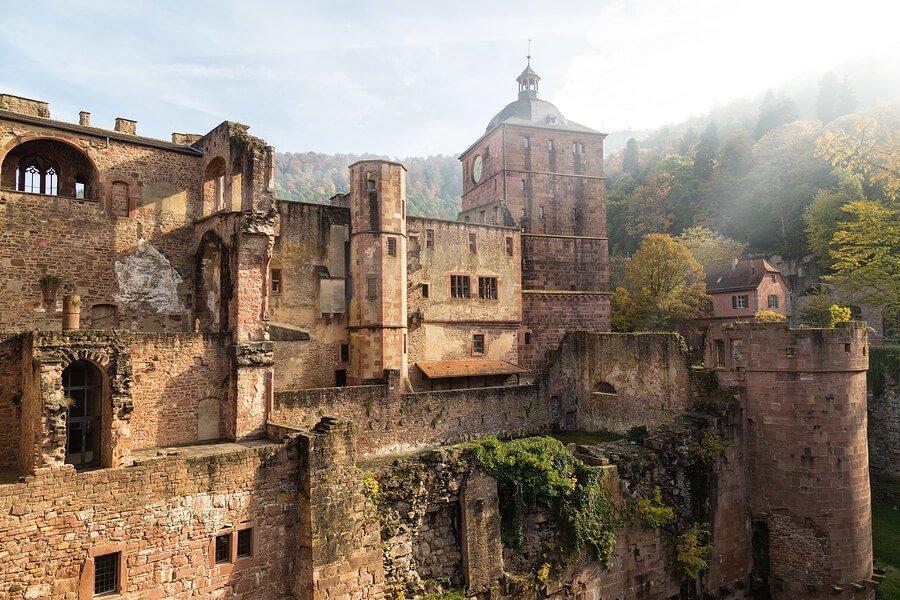
In ancient times, the window was primarily used to bring fresh air into the home, so an opening was crudely cut in the walls of the residence. While it may have been possible for men to survive during bad weather or fight off any predators with just a hole in the wall, bringing women and children forced the introduction of animal hides or cloth window treatments.
These flimsy materials offered little protection and eventually led to a more practical product, wood. Wood shutters, although still used today, were unhinged wood pieces that could be moved for ventilation or closed tight to keep the inside dry and secure. In either case, it took time and heavy lifting to “open a window.”
As early as the 14th century, translucent materials like flattened pieces of animal horn or glassy pebbles were used to let light enter without completely removing the shutters. Unfortunately, they weren’t very transparent which could present any number of problems.
Glass Evolution
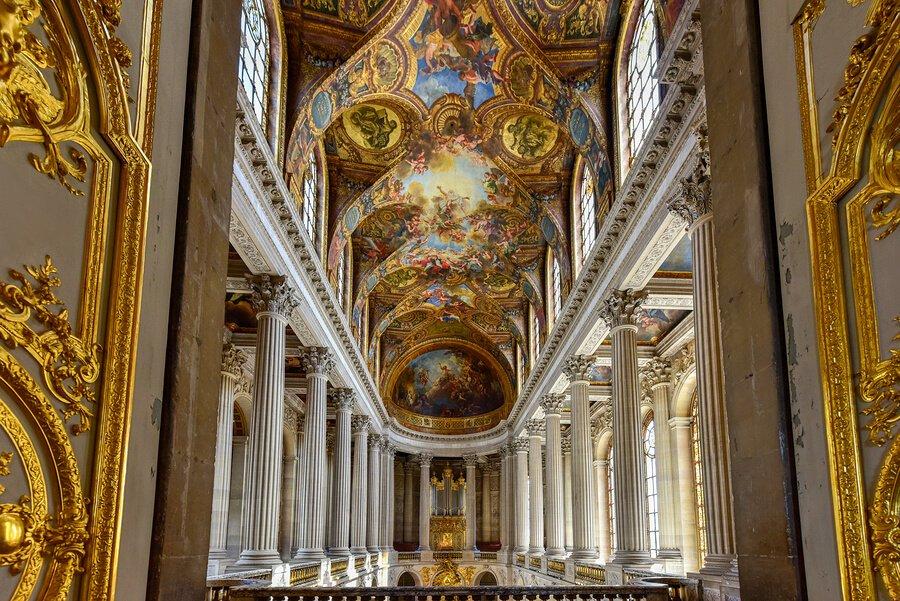
While average residents had to be content with makeshift coverings, glassmaking in Rome was being refined. It started with glass makers slicing cylindrical bubbles of glass, cutting them lengthwise and then flattening them out. Also known as broadsheet glass, the panes were full of imperfections such as bubbles and track lines that made large windows impossible to see through.
Sadly, the method for making glass windows was lost during the Dark Ages. But, with the 14th Century came a whole new generation of skilled, European glassblowers determined to reclaim their craft. By 1680, the Palace of Versailles in France was opened with spectacular window walls that exemplified how windows should be made.
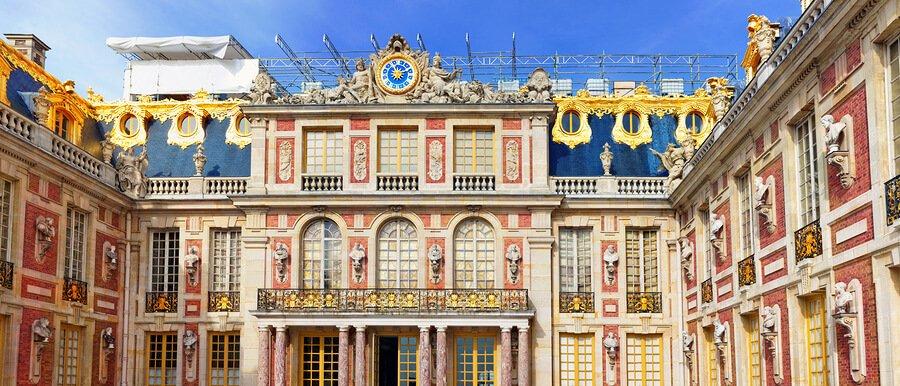
While it was becoming more common to see window glass by the mid-16th Century, it was a luxury few could justify. It wasn’t until the 17th Century that ordinary households were able to regularly using glass in their windows.
Changes in manufacturing processes steadily helped produce clearer, less expensive and ultimately, more energy efficient and safer replacement windows:
Crown Glass
Due to the poor quality and inability to use broadsheet glass in larger windows, a new and improved process made in France called crown glass was used. This was also a type of blown glass. It was opened from the end away from the blowpipe and moved in a circular motion to form window glass. The end result was much better clarity than broadsheet glass, but due to the exorbitant price, people stopped using it.
Polished Plate Glass
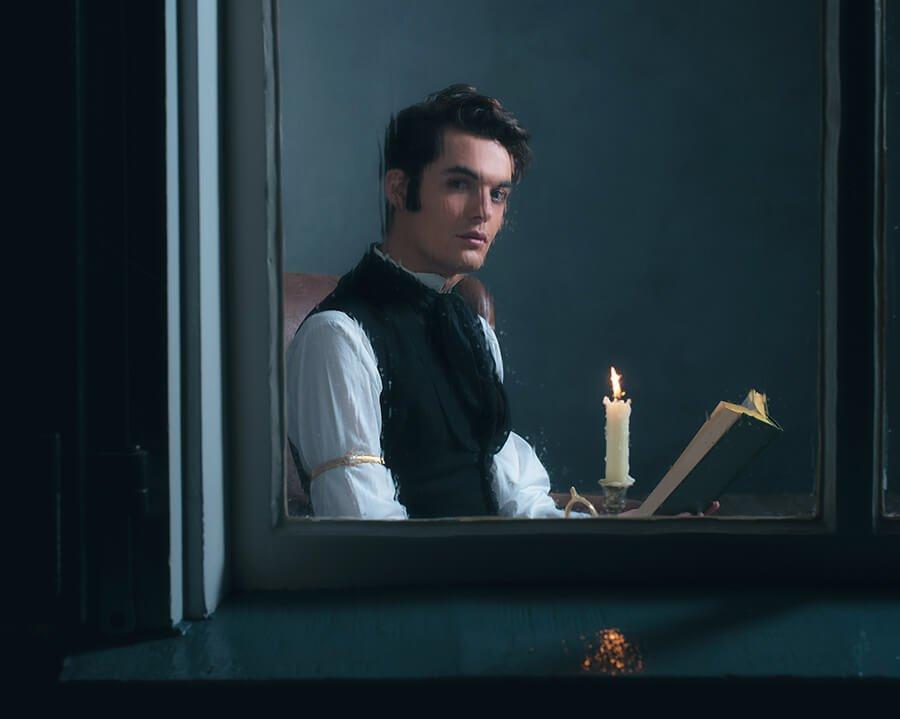
Popular in the late 18th Century, polished plate glass was made by casting a glass sheet on a solid surface. Hand-grinding and polishing were used to give it shape. This could be made into larger sizes but was it was labour-intensive, and therefore, expensive. Only wealthy people could afford the luxury of polished plate glass windows.
Laminated Glass
The process of adding a thin film of plastic between two glass pieces was introduced at the start of the 19th Century. It was safer and stronger than any window glass produced in the past. It was so popular that manufacturers in the 20th Century adopted the process to mass produce larger glass sheets and significantly reduce the cost.
Insulated Glass
In 1945, window manufacturer PPG created the first insulated glass window unit. It put two pieces of glass together with dead air space between. Eventually, other manufacturers or fabricators put gas inside the air space to improve their thermal effectiveness. Andersen Windows challenged the market by using a Freon-type gas and then a carbon dioxide combo. Today, argon and krypton gases are the standard for replacement windows.
Low-Emissivity Glass
Low-e reflective coatings became available in 1989 and was immediately accepted as one of the most energy-efficient means of filtering out the radiant spectrum of light. This improves thermal performance and reflectivity without affecting transparency.
Structural Changes
While window glass was making a transformation, window manufacturers were experimenting with different frame materials and window types. The original double-hung windows were built on site with wood. Andersen Windows was a pioneer in the industry and sold the first fully assembled casement window in 1937. This led to a large influx of customers wanting factory-made products.
New advances in steel and aluminum meant big things for commercial construction. By using steel frame to support large skyscrapers, the walls no longer bore the weight of the building. This meant entire walls of glass could be made without worry of collapse.
Replacement Windows
Before the 1970, windows were generally repaired instead of replaced. In situations where a replacement was needed, it would have been a full-frame product.
Without much focus on saving energy, storm windows were added as another layer of protection from outside elements. Window replacements were expensive (if you could even get an after-market replacement,) and there was little incentive to spend the money for a future “return on investment.”
Then, things changed. The energy crisis hit, energy costs were skyrocketing, and replacement windows were created to improve energy efficiency. Retrofit products followed a few years later making the process easier and less expensive. While full-frame replacements were still needed, they were not the primary request.
Installers
Specialty replacement installers were in high demand to make sure the windows were installed correctly. While some homeowners were capable of handling the project on their own, some projects warranted the expertise of an installer. This extra work helped establish an entirely new industry—replacement windows.
What’s Ahead
While windows are still made of traditional materials like wood, aluminum or steel, very little else has changed in the industry. New technologies are emerging every day that will change how the replacement industry operates. Time will only tell whether or not new practices will adapt to old-school methods to create an even more energy-efficient product.
Read Next:
5 Emerging Window Technologies That Are Hard to Believe Are Real
If you’re in the market for replacement windows, make sure you call on Ecoline Windows to do a whole-house evaluation. Their technicians are experienced and will guide you toward the best energy-saving option for your needs.
Liked the article? Share it!